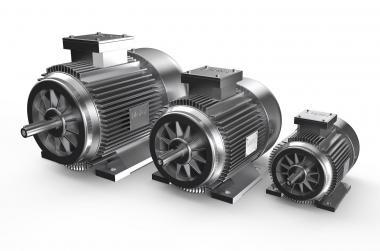
Silnik stacjonarny
Choć romantyczna era pary już dawno minęła, tęsknimy za dawnymi czasami, kiedy mogliśmy zobaczyć wagony ciągnięte przez ogromne, wspaniałe lokomotywy, gorące walce parowe ubijające gruz drogowy czy dymiące lokomotywy pracujące na polach.
Pojedynczy stacjonarny silnik parowy służący do centralnego napędzania za pomocą układu napędu pasowego wszystkich maszyn lub krosien fabrycznych. Jej kocioł palił zwykły węgiel.Może szkoda, że takich maszyn nie zobaczymy poza muzeum, ale istnieje możliwość zbudowania drewnianego modelu maszyny stacjonarnej. к To wielka przyjemność mieć w domu taki drewniany telefon, mobilne urządzenie do pracy. Tym razem zbudujemy model bardziej złożonego niż dotychczas silnika parowego z synchronizatorem suwakowym. Do napędzania drewnianego modelu zamiast pary będziemy oczywiście używać sprężonego powietrza z domowej sprężarki.
Praca silnika parowego polega na uwolnieniu sprężonej pary wodnej, a w naszym przypadku sprężonego powietrza, do cylindra, po jednej lub drugiej stronie tłoka. Powoduje to zmienny ruch ślizgowy tłoka, który przenoszony jest poprzez korbowód i wał napędowy na koło zamachowe. Korbowód przekształca ruch posuwisto-zwrotny tłoka w ruch obrotowy koła zamachowego. Jeden obrót koła zamachowego osiąga się w dwóch skokach tłoka. Dystrybucja pary odbywa się za pomocą mechanizmu suwakowego. Regulacja rozrządu odbywa się za pomocą mimośrodu zamontowanego na tej samej osi co koło zamachowe i korba. Płaski suwak zamyka i otwiera kanały wprowadzenia pary do cylindra, jednocześnie umożliwiając usunięcie zużytej rozprężonej pary.
Narzędzia: Piła Trichinella, brzeszczot do metalu, wiertarka elektryczna na stojaku, wiertarka stołowa, szlifierka taśmowa, szlifierka oscylacyjna, Dremel z nasadkami do drewna, wyrzynarka, pistolet do klejenia z klejem na gorąco, wiertła stolarskie 8, 11 i 14 mm. Przydadzą się również skrobaki lub pilniki do drewna. Do napędzania modelu użyjemy domowego kompresora lub bardzo mocnego odkurzacza, którego dysza wydmuchuje powietrze.
Materiały: deska sosnowa o szerokości 100 mm i grubości 20 mm, rolki o średnicy 14 i 8 mm, deska 20 na 20 mm, deska 30 na 30 mm, deska 60 na 8 mm, sklejka o grubości 4 i 10 mm. Wkręty do drewna, gwoździe 20 i 40 mm. Bezbarwny lakier w sprayu. Smar silikonowy lub olej maszynowy.
Podstawa maszyny. Ma wymiary 450 na 200 na 20 mm. Zróbmy go z dwóch kawałków desek sosnowych i sklejmy je dłuższymi bokami lub z jednego kawałka sklejki. Wszelkie nierówności na desce oraz miejsca powstałe po cięciu należy wygładzić papierem ściernym.
Wspornik osi koła zamachowego. Składa się z pionowej deski i przykrywającej ją od góry deski. Otwór na ośkę drewnianą wierci się w miejscu styku ich powierzchni po skręceniu. Będziemy potrzebować dwóch zestawów identycznych elementów. Podpory wycinamy z desek sosnowych o wymiarach 150 na 100 na 20 mm i listew o przekroju 20 na 20 i długości 150 mm. W listwach w odległości 20 mm od krawędzi wywierć otwory o średnicy 3 mm i wywierć je wiertłem o średnicy 8 mm, tak aby łby śrub można było łatwo ukryć. Wiercimy również otwory o średnicy 3 mm w przedniej stronie desek, aby można było przykręcić deski. W miejscu styku za pomocą wiertła 14 mm wywierć otwory na oś koła zamachowego. Obydwa elementy dokładnie obrabiamy papierem ściernym, najlepiej szlifierką oscylacyjną. Nie zapomnij również oczyścić otworów na drewnianą oś z wałka za pomocą walcowanego papieru ściernego. Oś powinna obracać się z minimalnym oporem. Powstałe w ten sposób podpory są demontowane i pokrywane bezbarwnym lakierem.
Koło zamachowe. Zaczniemy od narysowania struktury koła na zwykłym papierze.Nasze koło zamachowe ma całkowitą średnicę 200 mm i sześć szprych. Zostaną one utworzone w taki sposób, że narysujemy na okręgu sześć prostokątów obróconych o 60 stopni względem osi okręgu. Zacznijmy od narysowania okręgu o średnicy 130 mm, następnie zaznaczamy szprychy o grubości 15 mm.. W rogach powstałych trójkątów rysujemy koła o średnicy 11 mm. Połóż papier z narysowaną na sklejce strukturą koła i najpierw za pomocą dziurkacza zaznacz środki wszystkich małych okręgów oraz środek okręgu. Te wgniecenia zapewnią dokładność wiercenia. Narysuj okrąg, piastę i koło w miejscu, gdzie szprychy kończą się na parze zacisków, bezpośrednio na sklejce. Wszystkie rogi trójkątów wiercimy wiertłem o średnicy 11 mm. Za pomocą ołówka zaznacz na sklejce obszary, które powinny być puste. Uchroni nas to przed popełnianiem błędów. Za pomocą wyrzynarki lub piły do trichomów możemy odciąć zaznaczony wcześniej nadmiar materiału z koła zamachowego, co zaowocuje efektownymi drutami. Za pomocą pilnika lub noża cylindrycznego, ściągacza, a następnie Dremela wygładzamy ewentualne niedokładności i fazujemy krawędzie szprych.
Obręcz koła zamachowego. Będziemy potrzebować dwóch identycznych felg, które przykleimy po obu stronach koła zamachowego. Wytniemy je również ze sklejki o grubości 10 mm. Koła mają średnicę zewnętrzną 200 mm. Rysujemy je na sklejce za pomocą kompasu i wycinamy wyrzynarką. Następnie rysujemy współosiowo okrąg o średnicy 130 mm i wycinamy jego środek. Będzie to obręcz koła zamachowego, czyli jego obręcz. Wieniec powinien swoim ciężarem zwiększać bezwładność obracającego się koła. Za pomocą kleju wikol pokrywamy koło zamachowe, tj. ta z drutami, z wiankami po obu stronach. Wywierć otwór o średnicy 6 mm w środku koła zamachowego, aby włożyć w środek śrubę M6. W ten sposób otrzymamy zaimprowizowaną oś obrotu koła. Po zamontowaniu tej śruby jako osi koła w wiertarce, szybko obrabiamy kołowrotek, najpierw grubym, a następnie drobnym papierem ściernym. Radzę zmienić kierunek obrotów wiertarki, aby śruba koła się nie poluzowała. Koło powinno mieć gładkie krawędzie, a po obróbce na naszej pseudotokarce powinno obracać się płynnie, nie uderzając nim na boki. Jest to bardzo ważne kryterium jakości koła zamachowego. Po osiągnięciu tego celu usuń tymczasową śrubę i wywierć otwór na oś o średnicy 14 mm.
Cylinder maszynowy. Wykonane ze sklejki o grubości 10mm. Zaczniemy od dolnej i górnej części o wymiarach 140 x 60 oraz tylnej i przedniej części o wymiarach 60 x 60 mm. Wywierć otwory o średnicy 14 mm w środku tych kwadratów. Elementy te sklejamy klejem na gorąco z pistoletu do klejenia, tworząc w ten sposób rodzaj cylindrycznej ramy. Odpowiednie części należy przymocować prostopadle i równolegle do siebie, dlatego podczas klejenia należy użyć podkładki ustalającej i przytrzymać je w tej pozycji, aż klej stwardnieje. Dobrze jest podczas klejenia włożyć wałek, który będzie pełnił funkcję tłoczyska, w otwory części tylnej i przedniej. Od dokładności tego sklejenia zależy przyszła poprawna praca modelu.
Tłok Wykonane ze sklejki o grubości 10 mm, o wymiarach 60 na 60 mm. Przeszlifuj krawędzie kwadratu drobnym papierem ściernym i sfazuj boki. Wywierć w tłoku otwór o średnicy 14 mm na tłoczysko. W górnej części tłoka wierci się prostopadle otwór o średnicy 3 mm na śrubę mocującą tłok do tłoczyska. Wywierć otwór wiertłem o średnicy 8 mm, aby ukryć łeb śruby. Śruba przechodzi przez tłoczysko, utrzymując tłok na miejscu.
tłoczysko. Wytnijmy walec o średnicy 14 mm. Jego długość wynosi 280 mm. Nakładamy tłok na tłoczysko i montujemy go w ramie tłoka. Najpierw jednak określamy położenie tłoka względem tłoczyska. Tłok przesunie się o 80 mm. Podczas przesuwania nie powinien sięgać do krawędzi otworów wlotowych i wylotowych tłoka, ale w położeniu neutralnym powinien znajdować się na środku cylindra, a tłoczysko nie powinno wypadać z przodu cylindra. Gdy znajdziemy to miejsce, zaznaczamy ołówkiem położenie tłoka względem tłoczyska i na koniec wiercimy w nim otwór o średnicy 3 mm.
Dystrybucja. To najbardziej złożona część naszej maszyny. Musimy odtworzyć kanały powietrzne od sprężarki do cylindra, z jednej strony na drugą stronę tłoka, a następnie z powietrza wylotowego z cylindra. Kanały te wykonamy z kilku warstw sklejki o grubości 4 mm. Pasek rozrządu składa się z pięciu płytek o wymiarach 140 na 80 mm. W każdej płytce wycinane są otwory zgodnie z kształtami pokazanymi na zdjęciu. Zacznijmy od narysowania potrzebnych szczegółów na papierze i wycięcia wszystkich szczegółów. Wzory płytek rysujemy flamastrem na sklejce, układając je tak, aby nie marnować materiału, a jednocześnie przy jak najmniejszym nakładzie pracy przy piłowaniu. Ostrożnie zaznacz zaznaczone miejsca na otwory pomocnicze i wytnij odpowiednie kształty za pomocą wyrzynarki lub spodarki. Na koniec wszystko wyrównujemy i oczyszczamy papierem ściernym.
Zamek błyskawiczny. Jest to deska ze sklejki o takim samym kształcie jak na zdjęciu. Najpierw wywierć otwory i wytnij je wyrzynarką. Pozostały materiał można wyciąć piłą do trichomów lub wyrzucić za pomocą stożkowego noża cylindrycznego lub narzędzia Dremel. Po prawej stronie zamka znajduje się otwór o średnicy 3 mm, w którym będzie umieszczona oś klamki mimośrodu.
Prowadnice slajdów. Suwak działa pomiędzy dwoma płozami, prowadnicą dolną i górną. Wykonamy je ze sklejki lub listew o grubości 4 mm i długości 140 mm. Przyklej prowadnice klejem Vicol do odpowiedniej następnej płytki rozrządu.
Korbowód. Wytniemy go w tradycyjnym kształcie, jak pokazano na zdjęciu. Ważna jest odległość między osiami otworów o średnicy 14 mm. Powinno być 40 mm.
Ramię korby. Wykonany jest z paska o wymiarach 30 na 30 mm i ma długość 50 mm. W bloku wiercimy otwór o średnicy 14 mm i otwór nieprzelotowy prostopadle do przodu. Przeszlifuj przeciwległy koniec bloku pilnikiem do drewna, szlifierką i papierem ściernym.
Uchwyt tłoczyska. Ma kształt litery U, wykonany z drewna o wymiarach 30 na 30 mm i ma długość 40 mm. Jego kształt możecie zobaczyć na zdjęciu. W przedniej części bloku wiercimy otwór o średnicy 14 mm. Za pomocą piły z brzeszczotem wykonaj dwa nacięcia i wykonaj szczelinę, w której będzie można wsunąć tłoczysko, za pomocą wiertarki i piły włośniczowej. Wiercimy otwór na oś łączącą korbę z tłoczyskiem.
Podpora cylindra. Będziemy potrzebować dwóch identycznych elementów. Z desek sosnowych wytnij podpory o wymiarach 90 x 100 x 20 mm.
Ekscentryczność. Ze sklejki o grubości 4 mm wytnij cztery prostokąty o wymiarach 40 na 25 mm każdy. Otwory w prostokątach wiercimy wiertłem 14 mm. Ekscentryczny projekt pokazano na zdjęciu. Otwory te rozmieszczone są wzdłuż osi podłużnej, lecz są przesunięte względem siebie w osi poprzecznej o 8 mm. Łączymy prostokąty w dwie pary, sklejając je ze sobą powierzchniami. Przyklej cylinder o długości 28 mm do wewnętrznych otworów. Upewnijmy się, że powierzchnie prostokątów są do siebie równoległe. Pomóc nam w tym może klamka dźwigniowa.
ramię dźwignipołączenie suwaka z mimośrodem. Składa się z trzech części. Pierwszy to uchwyt w kształcie litery U, który zawiera suwak. W płaszczyźnie dla osi, wzdłuż której wykonuje ruch wahadłowy, wierci się otwór. Do drugiego końca przyklejony jest zacisk mimośrodowy. Zacisk ten jest demontowalny i składa się z dwóch bloków o wymiarach 20x20x50 mm każdy. Połącz bloki za pomocą wkrętów do drewna, a następnie wywierć otwór o średnicy 14 mm na krawędzi żebra na wał mimośrodowy. W jednym z bloków prostopadle do osi wiercimy ślepy otwór o średnicy 8 mm. Teraz możemy połączyć obie części wałkiem o średnicy 8 mm i długości około 160 mm, ale istotna jest odległość między osiami tych części, która powinna wynosić 190 mm.
Montaż maszyny. Za pomocą śruby zamontować tłok na tłoczysku włożonym w ramę cylindra i wywiercić na końcu otwór na oś korby. Pamiętaj, że otwór musi być równoległy do podstawy. Przyklej następujące elementy napędu rozrządu do ramy cylindra (zdjęcie a). Następna pierwsza płytka z czterema otworami (fot. b), druga z dwoma dużymi otworami (fot. c) łączy otwory w dwie pary. Następna jest trzecia płytka (zdjęcie d) z czterema otworami i nałóż na nią suwak. Na fotografiach (fot. e i f) widać, że suwak przesuwany podczas pracy przez mimośród kolejno odsłania jedną lub drugą parę otworów. Przyklej dwie prowadnice prowadzące suwak do trzeciej płytki od góry i od dołu. Mocujemy do nich ostatnią blaszkę dwoma otworami, zasłaniając suwak od góry (zdjęcie d). Przyklej blok z otworem przelotowym do górnego otworu o takiej średnicy, aby można było do niego przymocować wąż doprowadzający sprężone powietrze. Z drugiej strony cylinder jest zamknięty pokrywą przykręcaną kilkoma śrubami. Przyklej wsporniki osi koła zamachowego do podstawy, uważając, aby były one w linii i równolegle do płaszczyzny podstawy. Przed całkowitym montażem elementy i podzespoły maszyny pomalujemy lakierem bezbarwnym. Kładziemy korbowód na osi koła zamachowego i przyklejamy go dokładnie prostopadle do niego. Włóż oś korbowodu w drugi otwór. Obie osie muszą być do siebie równoległe. Po drugiej stronie podstawy przyklej dwie deski, aby utworzyć podporę dla cylindra. Przyklejamy do nich kompletny cylinder z mechanizmem rozrządu. Po sklejeniu cylindra zamontuj dźwignię łączącą suwak z mimośrodem. Dopiero teraz możemy określić długość dźwigni łączącej korbowód z tłoczyskiem. Odpowiednio wyciąć trzonek i przykleić uchwyty w kształcie litery U. Łączymy te elementy osiami wykonanymi z gwoździ. Pierwsza próba polega na ręcznym obróceniu osi koła zamachowego. Wszystkie ruchome części muszą poruszać się bez nadmiernego oporu. Korba wykona jeden obrót, a szpula powinna zareagować ruchem mimośrodowym.
Gra. Nasmaruj maszynę olejem w miejscach, w których spodziewamy się wystąpienia tarcia. Na koniec podłączamy model kablem do kompresora. Po uruchomieniu jednostki i doprowadzeniu sprężonego powietrza do cylindra nasz model powinien odpalić bez problemów dając konstruktorowi mnóstwo przyjemności. Wszelkie nieszczelności można załatać klejem z pistoletu do klejenia lub przezroczystym silikonem, ale dzięki temu nasz model będzie nieusuwalny. Cenną zaletą jest możliwość demontażu modelu, na przykład w celu zademonstrowania ruchu tłoka w cylindrze.
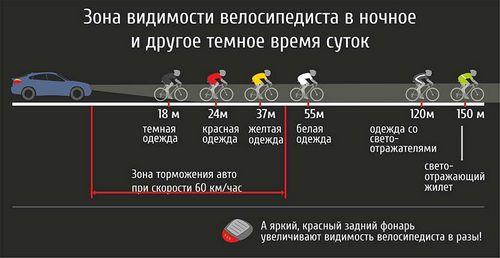
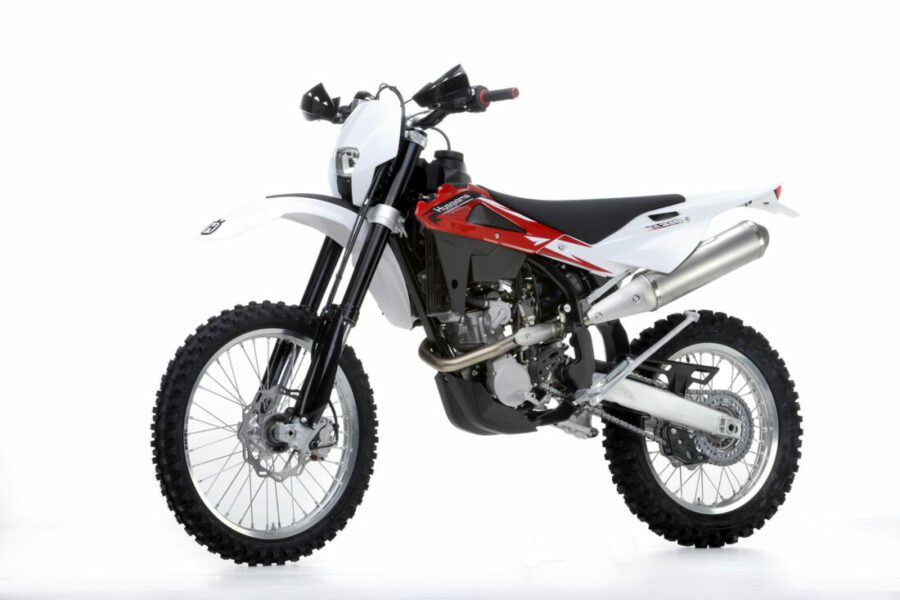