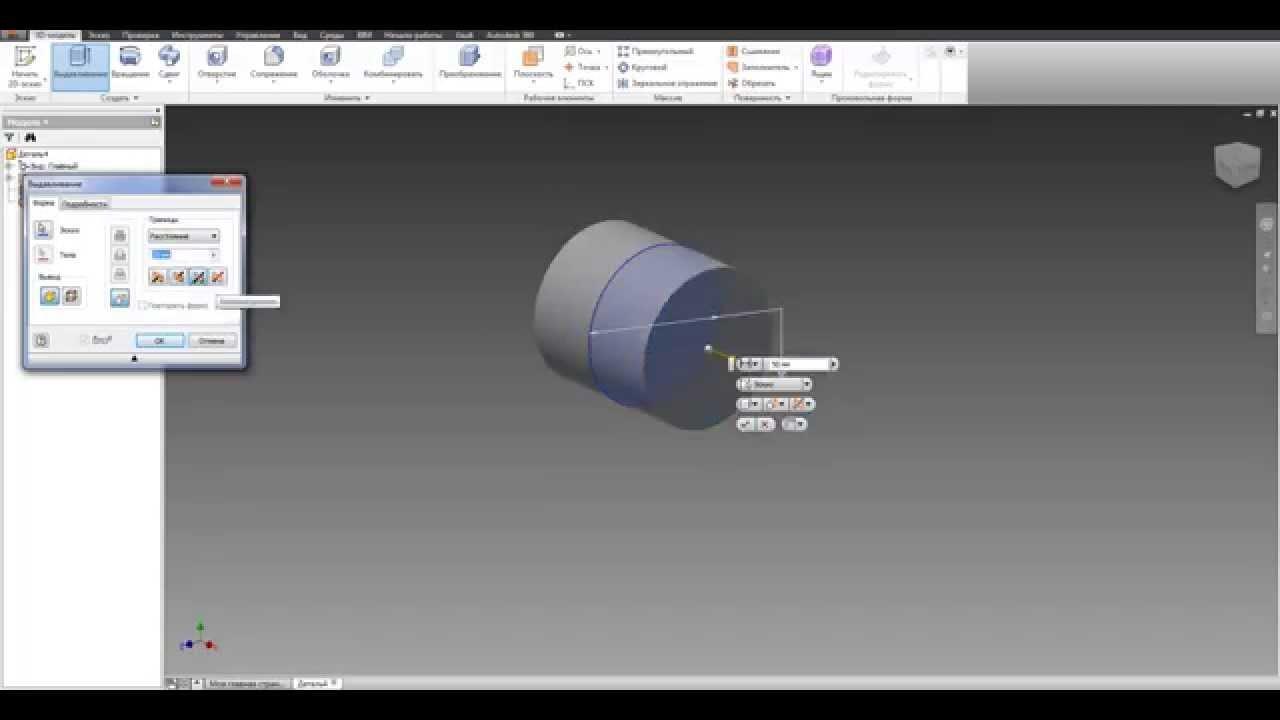
Kurs projektowania 3D w 360. Cylindry - lekcja 2
Zawartość
W pierwszej części kursu programowania 3D w Autodesk Fusion 360 zostaliśmy zapoznani z opcjami pozwalającymi na tworzenie prostych kształtów. Próbowaliśmy sposobów dodawania do nich nowych elementów i robienia dziur. W drugiej części kursu nabyte umiejętności rozwiniemy o tworzenie ciał wirujących. Wykorzystując tę wiedzę stworzymy przydatne złącza np. do rur plastikowych często używanych w warsztatach (1).
1. Przykłady standardowych złączy do sieci wodociągowych.
Rury plastikowe są często stosowane w warsztatach domowych ze względu na ich szeroką dostępność i przystępną cenę. Na całym świecie powstają różnorodne konstrukcje rurowe o różnych średnicach – od słomek do napojów, poprzez rury do instalacji wodociągowych i elektrycznych, aż po systemy kanalizacyjne. Nawet przy złączach hydraulicznych i kolankach dostępnych w sklepach z artykułami rzemieślniczymi można wiele zrobić (2, 3).
2. Kilka modeli złączy stworzonych dla majsterkowiczów.
3. Można z nich stworzyć naprawdę niezwykłe projekty!
Możliwości są naprawdę ogromne, a dostęp do specjalnego rodzaju złączy jeszcze bardziej je zwielokrotnia. W krajach anglosaskich są na rynku specjalnie zaprojektowane złącza – ale kupowanie ich za granicą poważnie podważa ekonomiczny sens całego przedsięwzięcia… Nic! W końcu możesz łatwo zaprojektować i wydrukować w domu nawet te akcesoria, których nie można kupić w Ameryce! Po ostatniej lekcji naszego kursu nie powinno to stanowić problemu.
4. W praktyce będą to prawdopodobnie bardziej praktyczne modele.
Na początek coś prostego - złącze zwane sprzęgłem
Jest to najprostszy element złączny. Podobnie jak w poprzedniej lekcji polecam zacząć od stworzenia szkicu na jednej z płaszczyzn, rysując okrąg o środku w środku układu współrzędnych. Średnica jego końców powinna odpowiadać wielkości wewnętrznej średnicy rur, które planujemy podłączyć (w opisywanym przypadku będą to rury elektryczne o średnicy 26,60 mm - cieńsze, tańsze niż hydraulika, ale wyjątkowo kiepskie kształtki odpowiedni dla majsterkowiczów).
5-6. Wymiana nawet głównych łączników systemu na własne - wewnętrzne - sprawi, że połączenia będą bardziej estetyczne, umożliwi lepszy montaż dowolnych obudów czy okładzin - a do tego wyjdzie dużo taniej!
Korzystając z opcji znanej już z poprzedniej lekcji, okrąg należy narysować w górę. W oknie pomocniczym znajdź parametr i zmień jego ustawienie na Symetryczny. Należy dokonać tej zmiany przed zatwierdzeniem funkcji pełnego wytłoczenia. Dzięki temu projektowany łącznik będzie miał środek na płaszczyźnie szkicu (7). Przyda się to w następnym kroku.
Teraz tworzymy drugi szkic w tej samej płaszczyźnie, co poprzedni rysunek. Pierwszy szkic zostanie automatycznie ukryty i będzie można go ponownie wyświetlić, odnajdując zakładkę w drzewku po lewej stronie. Po rozwinięciu pojawi się lista wszystkich szkiców w projekcie - kliknij żarówkę obok nazwy szkicu, a wybrany szkic stanie się ponownie widoczny.
Następny okrąg również powinien być wyśrodkowany w środku układu współrzędnych. Tym razem jego średnica wyniesie 28,10 mm (odpowiada to zewnętrznej średnicy rur). W oknie pomocniczym zmień tryb tworzenia bryły z wycinania na dodawanie (funkcja jest ostatnim parametrem w oknie). Czynność powtarzamy jak z poprzednim okręgiem, ale tym razem wartość wyciągnięcia nie musi być duża (wystarczy kilka milimetrów).
8. Proste sterowanie – znane z poprzedniej edycji kursu.
9. Sprzęgło gotowe i otynkowane.
Złącze byłoby gotowe, ale warto zmniejszyć ilość plastiku potrzebnego do jego wydrukowania – tak jest zdecydowanie bardziej ekonomicznie i bardziej ekologicznie! Wydrążamy więc środek łącznika - na złączkę wystarczy ścianka kilku mm. Można to zrobić w taki sam sposób, jak w przypadku dziurki od kółka na klucze z poprzedniej części kursu.
Zaczynając szkicować okrąg, rysujemy okrąg na jednym końcu łącznika i przecinamy go przez cały model. Od razu lepiej (9)! Projektując modele do druku warto również wziąć pod uwagę dokładność drukarki i uwzględnić to w gabarytach projektu. Zależy to jednak od użytego sprzętu, dlatego nie ma jednej reguły, która sprawdzi się w każdym przypadku.
Czas na coś bardziej wymagającego – kolano 90°.o
Projektowanie tego elementu zaczniemy od szkicu na dowolnej płaszczyźnie. W tym przypadku również warto zacząć od środka układu współrzędnych. Zaczniemy od narysowania dwóch równych linii prostopadłych do siebie. Pomoże w tym siatka na tle arkusza, do której „przyklejają się” narysowane linie.
10. Utwórz ścieżkę dla łokcia.
Utrzymanie równych linii za każdym razem może być kłopotliwe, szczególnie jeśli jest ich więcej. Na ratunek przychodzi pomocnicze okienko przyklejone do prawej strony ekranu (domyślnie można je zminimalizować). Po rozwinięciu (za pomocą dwóch strzałek nad tekstem) pojawiają się dwie listy: .
11. Dodaj profil klasyczny.
Po wybraniu obu narysowanych linii szukamy opcji Równe do na drugiej liście. Po kliknięciu można ustawić stosunek długości linii. Na rysunku obok linii pojawi się znak „=”. Pozostaje zaokrąglić szkic, aby przypominał łokieć. Skorzystamy z opcji z rozwijanej listy zakładki. Po wybraniu tej opcji należy kliknąć punkt połączenia rysowanych linii, wpisać wartość promienia i zatwierdzić wybór klawiszem Enter. Tak powstaje tzw. tor.
12. Przytnij tak, aby łącznik zmieścił się w rurce.
Teraz będziesz potrzebować profilu łokciowego. Zamknij bieżący szkic klikając opcję z ostatniej zakładki (). Stwórzmy jeszcze raz nowy szkic - tutaj kluczowy jest wybór płaszczyzny. Powinna to być płaszczyzna prostopadła do tej, na której znajdował się poprzedni szkic. Rysujemy okrąg (o średnicy 28,10 mm) podobnie jak poprzednie (ze środkiem w środku układu współrzędnych) i jednocześnie na początku narysowanej wcześniej ścieżki. Po narysowaniu okręgu zamknij szkic.
13. Takie kolanko rzeczywiście mogłoby łączyć rury - tylko po co tyle plastiku?
Wybierz opcję z listy rozwijanej karty. Otworzy się okno pomocnicze, w którym musimy wybrać profil i ścieżkę. Jeżeli miniaturki znikną z obszaru roboczego, można je wybrać z drzewka po lewej stronie zakładki.
W okienku pomocniczym podświetlona jest opcja obok napisu - czyli wybieramy profil, czyli drugi szkic. Następnie kliknij przycisk „Wybierz” poniżej i wybierz ścieżkę, tj. pierwszy szkic. Potwierdzenie operacji tworzy kolano. Oczywiście średnica profilu może być dowolna – w przypadku kolanka stworzonego na potrzeby tego artykułu jest to 28,10 mm (jest to średnica zewnętrzna rury).
14. Kontynuujemy temat – w końcu warto pamiętać zarówno o ekologii, jak i ekonomii!
Chcemy, aby tuleja weszła w rurę (12), więc jej średnica powinna być taka sama jak średnica rury wewnętrznej (w tym przypadku 26,60 mm). Efekt ten możemy osiągnąć podcinając nogawki do łokcia. Na końcach kolanka rysujemy okrąg o średnicy 26,60 mm, a drugi okrąg ma już średnicę większą niż zewnętrzna średnica rur. Tworzymy wykrój, który dotnie łącznik do odpowiedniej średnicy, pozostawiając zagięty fragment kolanka o zewnętrznej średnicy rury.
Powtarzamy tę procedurę na drugiej nodze łokcia. Podobnie jak w przypadku pierwszego łącznika, teraz zmniejszymy kolano. Wystarczy skorzystać z opcji znajdujących się na karcie. Po wybraniu tej opcji należy wybrać końcówki, które mają być puste i określić szerokość wykonywanej obręczy. Omawiana funkcja usuwa jedną ściankę i tworzy z naszego modelu „skorupę”.
Zrobiony?
Voila! Łokieć gotowy (15)!
15. Wizualizacja gotowego łokcia.
OK, rozumiemy! Co dalej?
Obecna lekcja, prezentując zasady tworzenia prostych, jednocześnie otwiera możliwość realizacji podobnych projektów. „Produkcja” bardziej skomplikowanych elementów złącznych jest tak prosta, jak opisano powyżej (18). Polega na zmianie kątów pomiędzy liniami ścieżki lub doklejeniu kolejnego kolanka. Operację wytłoczenia środkowego wykonujemy na samym końcu konstrukcji. Przykładem są łączniki sześciokątne (lub klucze imbusowe), a uzyskujemy je poprzez zmianę kształtu profilu.
16. Dzięki poznanym właśnie funkcjom możesz także utworzyć na przykład klucz sześciokątny...
Dysponujemy gotowymi modelami i możemy je zapisać do pliku o równoważnym formacie (.stl). Zapisany w ten sposób model można otworzyć w specjalnym programie, który przygotuje plik do druku. Jednym z najpopularniejszych i darmowych programów tego typu jest wersja w języku polskim.
17.… lub inny potrzebny łącznik - procedury są prawie takie same!
18. Przykład konektora utworzonego z wykorzystaniem operacji z bieżącej lekcji.
Po zainstalowaniu poprosi nas o aplikację. Posiada bardzo przejrzysty interfejs i nawet osoba uruchamiająca program po raz pierwszy bez problemu poradzi sobie z przygotowaniem modelu do druku. Otwórz plik z modelem (Plik → Otwórz plik), w prawym panelu ustaw materiał z którego będziemy drukować, określ dokładność oraz ustaw dodatkowe opcje poprawiające jakość druku – wszystkie zostają dodatkowo opisane po najechaniu na napis przycisk.
19. Mały podgląd tematu kolejnej lekcji.
Wiedząc jak zaprojektować i wydrukować stworzone modele, pozostaje jedynie przetestować zdobytą wiedzę. Z pewnością przyda się to na przyszłych lekcjach – komplet tematów dla całego kursu przedstawia poniższa tabela.
Plan kursu 3 Projektowanie 360D
• Lekcja 1: Przeciąganie sztywnych brył (breloczków)
• Lekcja 2: Ciała stałe (złącza rur)
• Lekcja 3: Ciała sferyczne (łożyska)
• Lekcja 4: Złożone bryły sztywne (elementy konstrukcyjne robotów)
• Lekcja 5: Proste mechanizmy na raz! (przekładnie kątowe).
• Lekcja 6: Modele prototypowe (model żurawia budowlanego)
Zobacz także:

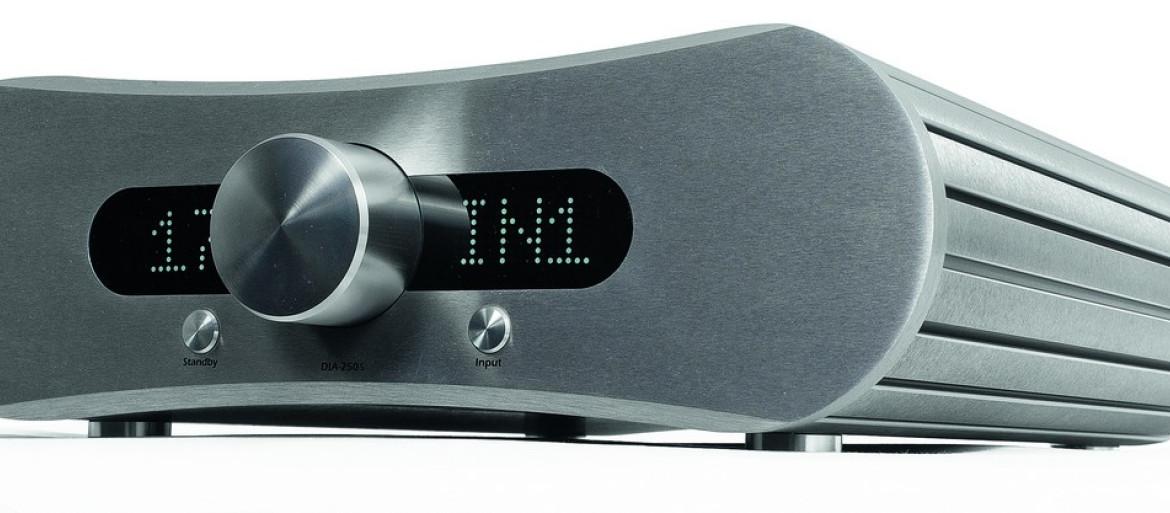