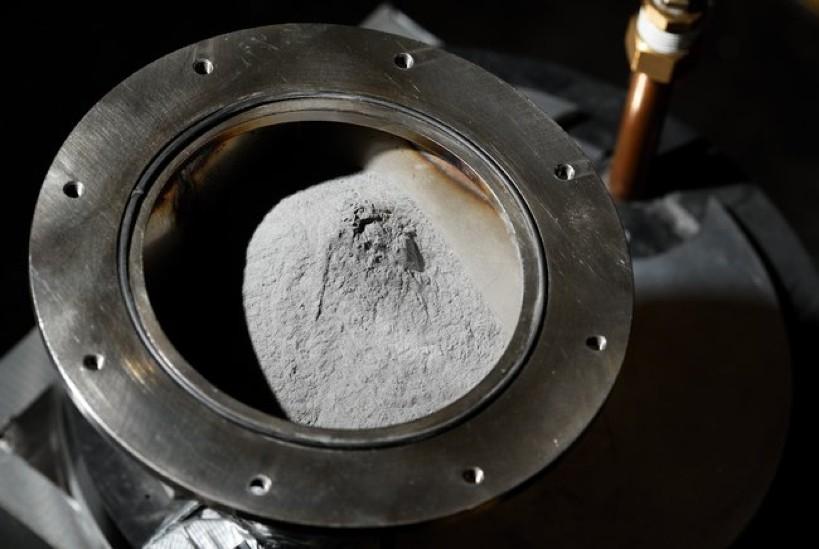
Przyszłość w proszku
Szwedzka firma VBN Components wykonuje wyroby stalowe w technologiach addytywnych z wykorzystaniem proszku z dodatkami, głównie narzędzi takich jak wiertła i frezy. Technologia druku 3D eliminuje potrzebę kucia i obróbki skrawaniem, zmniejsza zużycie surowców i zapewnia użytkownikom końcowym większy wybór wysokiej jakości materiałów.
Oferta komponentów VBN obejmuje m.in. Wibenit 290która według szwedzkiej firmy jest najtwardszą stalą na świecie (72 HRC). Proces tworzenia Vibenite 290 polega na stopniowym zwiększaniu twardości materiałów aż do. Po wydrukowaniu pożądanych części z tego surowca nie jest wymagana żadna dalsza obróbka poza szlifowaniem lub EDM. Nie wymaga cięcia, frezowania ani wiercenia. W ten sposób firma tworzy części o wymiarach do 200 x 200 x 380 mm, których geometrii nie można wyprodukować przy użyciu innych technologii wytwarzania.
Stal nie zawsze jest potrzebna. Zespół badawczy z HRL Laboratories opracował rozwiązanie do drukowania 3D. stopy aluminium z dużą wytrzymałością. Nazywa się to metoda nanofunkcyjna. Najprościej mówiąc, nowa technika polega na nakładaniu na drukarkę 3D specjalnych nanofunkcyjnych proszków, które następnie są „spiekane” laserowo cienkimi warstwami, co prowadzi do wzrostu trójwymiarowego obiektu. Podczas topienia i krzepnięcia powstałe struktury nie ulegają zniszczeniu i zachowują pełną wytrzymałość dzięki nanocząsteczkom pełniącym rolę centrów zarodkowania dla zamierzonej mikrostruktury stopu.
Stopy o wysokiej wytrzymałości, takie jak aluminium, są szeroko stosowane w przemyśle ciężkim, technice lotniczej (np. kadłuby) i częściach samochodowych. Nowa technologia nanofunkcjonalizacji nadaje im nie tylko wysoką wytrzymałość, ale także różnorodność kształtów i rozmiarów.
Dodawanie zamiast odejmowania
W tradycyjnych metodach obróbki metali odpady są usuwane przez obróbkę skrawaniem. Proces addytywny działa odwrotnie – polega na nakładaniu i dodawaniu kolejnych warstw niewielkich ilości materiału, tworząc części XNUMXD o niemal dowolnym kształcie na podstawie modelu cyfrowego.
Chociaż technika ta jest już szeroko stosowana zarówno do prototypowania, jak i odlewania modeli, jej zastosowanie bezpośrednio w produkcji wyrobów lub urządzeń przeznaczonych na rynek było utrudnione ze względu na niską wydajność i niezadowalające właściwości materiału. Jednak ta sytuacja stopniowo się zmienia dzięki pracy badaczy w wielu ośrodkach na całym świecie.
Dzięki żmudnym eksperymentom ulepszono dwie główne technologie drukowania XNUMXD: laserowe osadzanie metali (LMD) i selektywne topienie laserowe (ULM). Technologia laserowa umożliwia precyzyjne wykonanie drobnych detali oraz uzyskanie dobrej jakości powierzchni, co nie jest możliwe przy druku wiązką elektronów 50D (EBM). W SLM końcówka wiązki lasera jest kierowana na proszek materiału, lokalnie zgrzewając go według zadanego wzoru z dokładnością od 250 do 3 mikronów. Z kolei LMD wykorzystuje laser do obróbki proszku w celu stworzenia samonośnych struktur XNUMXD.
Metody te okazały się bardzo obiecujące w tworzeniu części samolotów. aw szczególności laserowe osadzanie metalu rozszerza możliwości projektowania komponentów lotniczych. Mogą być wykonane z materiałów o złożonej strukturze wewnętrznej i nachyleniu, które nie były możliwe w przeszłości. Ponadto obie technologie laserowe umożliwiają tworzenie wyrobów o złożonej geometrii oraz uzyskiwanie rozszerzonej funkcjonalności wyrobów z szerokiej gamy stopów.
We wrześniu ubiegłego roku Airbus ogłosił, że wyposażył swój produkcyjny A350 XWB w druk addytywny. wspornik tytanowy, wyprodukowany przez firmę Arconic. To nie koniec, bo umowa Arconic z Airbusem przewiduje druk 3D z proszku tytanowo-niklowego. części ciała i układ napędowy. Należy jednak zaznaczyć, że Arconic nie wykorzystuje technologii laserowej, a własną ulepszoną wersję elektronicznego łuku EBM.
Jednym z kamieni milowych w rozwoju technologii addytywnych w obróbce metali będzie prawdopodobnie pierwszy w historii prototyp zaprezentowany w siedzibie holenderskiej grupy Damen Shipyards jesienią 2017 roku. śmigło statku stop metali nazwany imieniem VAAMpeller. Po odpowiednich testach, z których większość już się odbyła, model ma szansę zostać dopuszczony do użytku na statkach.
Ponieważ przyszłość technologii obróbki metali leży w proszkach stali nierdzewnej lub komponentach stopowych, warto poznać głównych graczy na tym rynku. Według „Additive Manufacturing Metal Powder Market Report” opublikowanego w listopadzie 2017 roku, najważniejsi producenci proszków metali do druku 3D to: GKN, Hitachi Chemical, Rio Tinto, ATI Powder Metals, Praxair, Arconic, Sandvik AB, Renishaw, Höganäs AB, Metaldyne Performance Group, BÖHLER Edelstahl, Carpenter Technology Corporation, Aubert & Duval.
Nadruk śmigła WAAMpeller
Faza ciekła
Najbardziej znane technologie dodatków metalicznych polegają obecnie na wykorzystaniu proszków (tak powstaje wspomniany wibenit) „spiekanych” i topionych laserowo w wysokich temperaturach wymaganych dla materiału wyjściowego. Pojawiają się jednak nowe koncepcje. Naukowcy z Laboratorium Inżynierii Kriobiomedycznej Chińskiej Akademii Nauk w Pekinie opracowali metodę Druk 3D „atramentem”, składający się ze stopu metalu o temperaturze topnienia nieco powyżej temperatury pokojowej. W badaniu opublikowanym w czasopiśmie Science China Technological Sciences naukowcy Liu Jing i Wang Lei demonstrują technikę drukowania w fazie ciekłej stopów na bazie galu, bizmutu lub indu z dodatkiem nanocząstek.
W porównaniu z tradycyjnymi metodami prototypowania metali, druk 3D w fazie ciekłej ma kilka ważnych zalet. Po pierwsze, można osiągnąć stosunkowo wysoki wskaźnik wytwarzania struktur trójwymiarowych. Ponadto tutaj możesz bardziej elastycznie regulować temperaturę i przepływ chłodziwa. Ponadto płynny metal przewodzący można stosować w połączeniu z materiałami niemetalicznymi (takimi jak tworzywa sztuczne), co zwiększa możliwości projektowe złożonych elementów.
Naukowcy z American Northwestern University opracowali również nową technikę drukowania 3D z metalu, która jest tańsza i mniej złożona niż wcześniej znano. Zamiast proszku metalowego używa laserów czy wiązek elektronów konwencjonalny piekarnik i płynny materiał. Ponadto metoda ta sprawdza się dobrze w przypadku szerokiej gamy metali, stopów, związków i tlenków. Jest to podobne do uszczelnienia dyszy, które znamy z tworzyw sztucznych. „Atrament” składa się z metalicznego proszku rozpuszczonego w specjalnej substancji z dodatkiem elastomeru. W momencie aplikacji ma temperaturę pokojową. Następnie warstwa materiału nałożona z dyszy jest spiekana z poprzednimi warstwami w podwyższonej temperaturze wytworzonej w piecu. Technika została opisana w specjalistycznym czasopiśmie Advanced Functional Materials.
Chińska metoda drukowania w fazie ciekłego metalu
W 2016 roku naukowcy z Harvardu wprowadzili kolejną metodę, która umożliwia tworzenie metalowych konstrukcji XNUMXD. drukowane „w powietrzu”. Uniwersytet Harvarda stworzył drukarkę 3D, która w przeciwieństwie do innych nie tworzy obiektów warstwa po warstwie, ale tworzy złożone struktury „w powietrzu” – z błyskawicznie zamarzającego metalu. Urządzenie, opracowane w Szkole Inżynierii i Nauk Stosowanych im. Johna A. Paulsona, drukuje obiekty przy użyciu nanocząsteczek srebra. Skoncentrowany laser podgrzewa materiał i stapia go, tworząc różne struktury, takie jak helisa.
Zapotrzebowanie rynku na wysoce precyzyjne produkty konsumenckie drukowane w 3D, takie jak implanty medyczne i części silników lotniczych, szybko rośnie. A ponieważ dane produktów można udostępniać innym, firmy na całym świecie, jeśli mają dostęp do proszku metalicznego i odpowiedniej drukarki 3D, mogą pracować nad obniżeniem kosztów logistyki i zapasów. Jak wiadomo, opisane technologie znacznie ułatwiają wytwarzanie części metalowych o złożonej geometrii, wyprzedzając tradycyjne technologie produkcji. Rozwój specjalistycznych zastosowań prawdopodobnie doprowadzi do obniżenia cen i otwarcia na wykorzystanie druku 3D również w zastosowaniach konwencjonalnych.
Najtwardsza szwedzka stal - do druku 3D:
Najtwardsza stal na świecie - wyprodukowana w Uppsali w Szwecji
Folia aluminiowa do nadruku:
Przełom w metalurgii: druk 3D aluminium o wysokiej wytrzymałości

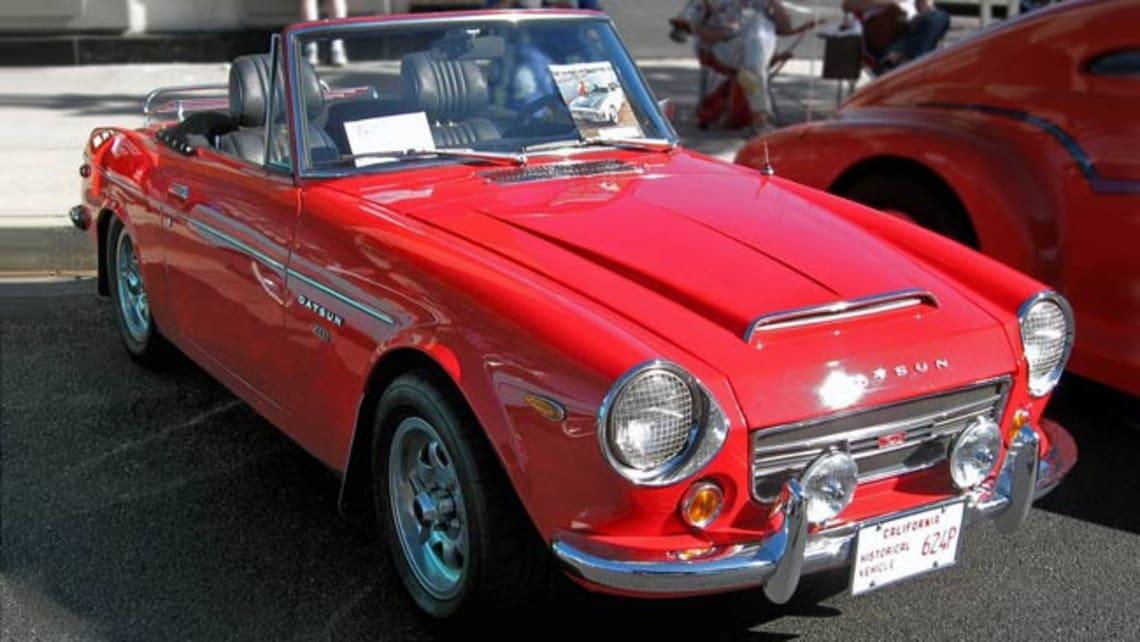
Jeden komentarz
Anonim
śmieszny