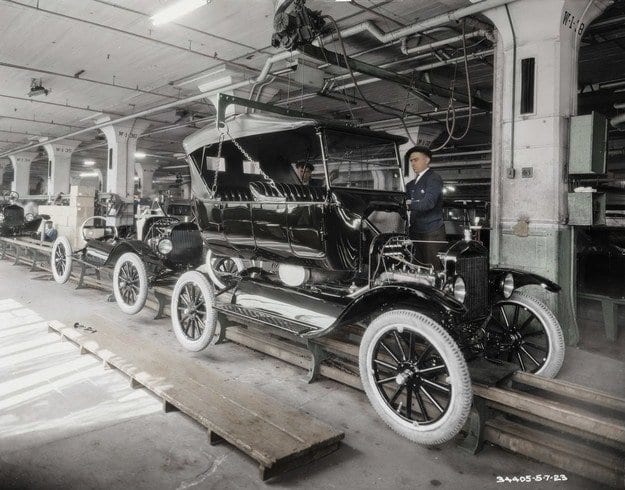
Kto ruszył przenośnikiem
Linie produkcyjne znów pracują, a to powód, by pamiętać o ich twórcy
7 października 1913 w jednej z hal fabryki samochodów Highland Park. Ford uruchamia pierwszą na świecie linię do produkcji samochodów. Materiał ten jest wyrazem szacunku dla innowacyjnych procesów produkcyjnych stworzonych przez Henry'ego Forda, który zrewolucjonizował motoryzację.
Organizacja produkcji samochodów jest dziś procesem bardzo złożonym. Montaż samochodu w fabryce to 15% całego procesu produkcyjnego. Pozostałe 85 procent to produkcja każdej z ponad dziesięciu tysięcy części i ich wstępny montaż w około 100 najważniejszych jednostkach produkcyjnych, które następnie trafiają na linię produkcyjną. Ta ostatnia jest realizowana przez ogromną liczbę dostawców (np. 40 000 w VW), którzy realizują bardzo złożony i bardzo wydajny skoordynowany łańcuch procesów produkcyjnych, w tym dokładne i terminowe dostawy (tzw. proces just-in-time ) komponentów i dostawców. pierwszy i drugi poziom. Rozwój każdego modelu to tylko część tego, jak dociera on do konsumentów. W organizację procesu produkcyjnego odbywającego się w równoległym wszechświecie zaangażowana jest ogromna liczba inżynierów, obejmująca działania od koordynacji dostaw komponentów po ich fizyczny montaż w fabryce przy pomocy ludzi i robotów.
Rozwój procesu produkcyjnego to zasługa prawie 110 lat ewolucji, jednak największy wkład w jego powstanie miał Henry Ford. Co prawda kiedy tworzył obecną organizację, Ford Model T, który zaczął być montowany był niezwykle prosty, a jego podzespoły były prawie w całości produkowane przez samą firmę, ale każda dziedzina nauki ma swoich pionierów, którzy kładli podwaliny niemal na ślepo . Henry Ford na zawsze zapisze się w historii jako człowiek, który zmotoryzował Amerykę – na długo przed tym, zanim stało się to w Europie – łącząc prosty i niezawodny samochód z wydajną produkcją, która obniżyła koszty.
Pioneer
Henry Ford zawsze wierzył, że ludzki postęp będzie napędzany naturalnym rozwojem gospodarczym opartym na produkcji, i nienawidził wszelkich spekulacyjnych form zysku. Nic dziwnego, że przeciwnik takich zachowań ekonomicznych będzie maksymalistą, a dążenie do wydajności i stworzenie linii produkcyjnej jest częścią jego historii sukcesu.
We wczesnych latach przemysłu motoryzacyjnego samochody były starannie składane przez wykwalifikowanych i zwykle utalentowanych inżynierów w skromnych warsztatach rzemieślniczych. W tym celu korzystają ze znanych dotychczas maszyn do montażu powozów i rowerów. Zasadniczo maszyna znajduje się w pozycji statycznej, a pracownicy i części poruszają się po niej. Prasy, wiertarki, spawarki są zgrupowane w różnych miejscach, a poszczególne gotowe produkty i komponenty są montowane na stołach warsztatowych, a następnie muszą „podróżować” z jednego miejsca do drugiego i do samego samochodu.
Nazwisko Henry'ego Forda nie można znaleźć wśród pionierów przemysłu samochodowego. Ale to dzięki kreatywnemu połączeniu unikalnych zdolności zarządczych, organizacyjnych i projektowych Henry'ego Forda samochód stał się zjawiskiem masowym i zmotoryzował naród amerykański. Swój uprzywilejowany status zawdzięcza jemu i dziesiątkom innych postępowych Amerykanów, a Model T z początku XX wieku nadał namacalny charakter dzisiejszemu stereotypowi, że samochód może być koniecznością, niekoniecznie luksusem. Samochód, który odgrywa w tym główną rolę, Model T, nie błyszczy niczym szczególnym, poza niesamowitą lekkością i wytrzymałością. Jednak metody Henry'ego Forda do tak wydajnej produkcji tego samochodu stały się podstawą nowej rewolucyjnej ideologii technicznej.
Do 1900 roku na świecie było już ponad 300 firm produkujących pojazdy z silnikami spalinowymi, a wiodącymi krajami w tej branży były Stany Zjednoczone, Francja, Niemcy, Anglia, Włochy, Belgia, Austria i Szwajcaria. W tamtym czasie przemysł naftowy rozwijał się w bardzo szybkim tempie, a teraz Ameryka była nie tylko głównym producentem czarnego złota, ale także liderem technologicznym w tej dziedzinie. Tworzy to wystarczająco stabilny stop, aby odrzucić rozwój przemysłu amerykańskiego.
Amerykański samochód
Gdzieś w tym zamieszaniu pojawia się nazwisko Henry Forda. W obliczu sprzeciwu partnerów swojej pierwszej firmy, który chciał wyprodukować praktyczny, niezawodny, tani i seryjny samochód, w 1903 roku założył własną firmę, którą nazwał Ford Motor Company. Ford zbudował samochód, aby wygrać wyścig, posadził za kierownicą ośmiodniowego rowerzystę iz łatwością zebrał 100 000 dolarów od życzliwych inwestorów na swój startup; bracia Dodge zgadzają się dostarczyć mu silniki. W 1905 roku był gotowy ze swoim pierwszym samochodem produkcyjnym, który nazwał Fordem Model A. Po wypuszczeniu na rynek kilku drogich modeli, postanowił wrócić do swojego pierwotnego pomysłu stworzenia popularnego samochodu. Kupując część akcji jej udziałowców, uzyskuje w firmie wystarczające możliwości finansowe i pozycje, aby rozpocząć własną produkcję.
Ford jest rzadkim ptakiem nawet dla liberalnego zrozumienia Amerykanów. Łaskotliwy, ambitny, miał własne pomysły na branżę samochodową, które w tamtym czasie znacznie różniły się od poglądów jego konkurentów. Zimą 1906 roku wynajął pokój w swojej fabryce w Detroit i spędził z kolegami dwa lata projektując i planując produkcję Modelu T. Samochód, który ostatecznie powstał w wyniku tajnej pracy zespołu Forda, zmienił się . obraz Ameryki na zawsze. Za 825 USD nabywca Modelu T może kupić samochód ważący zaledwie 550 kg ze stosunkowo mocnym czterocylindrowym silnikiem o mocy 20 KM, który jest łatwy w prowadzeniu dzięki sterowanej pedałami dwubiegowej przekładni planetarnej. Proste, niezawodne i wygodne, małe auto zachwyca ludzi. Model T był także pierwszym amerykańskim samochodem wykonanym z lżejszej stali wanadowej, nieznanej wówczas innym zagranicznym producentom. Ford przywiózł tę metodę z Europy, gdzie używano jej do produkcji luksusowych limuzyn.
We wczesnych latach Model T był produkowany jak wszystkie inne samochody. Jednak rosnące zainteresowanie nim i rosnący popyt skłoniły Forda do rozpoczęcia budowy nowego zakładu, a także zorganizowania wydajniejszego systemu produkcji. W zasadzie nie stara się o pożyczkę, ale o finansowanie swoich przedsięwzięć z własnych rezerw. Sukces samochodu pozwolił mu zainwestować w stworzenie wyjątkowej fabryki w Highland Park, nazwanej tak przez samego Rockefellera, której rafinerie są kryterium najnowocześniejszej produkcji „cudem przemysłowym swoich czasów”. Celem Forda jest uczynienie samochodu tak lekkim i prostym, jak to tylko możliwe, a zakup nowych części jest bardziej opłacalny niż ich naprawa. Prosty model T składa się z silnika ze skrzynią biegów, prostej ramy i nadwozia oraz dwóch elementarnych osi.
7 1913 października
We wczesnych latach produkcja w tym czterokondygnacyjnym zakładzie była zorganizowana odgórnie. „Opada” z czwartego piętra (gdzie montowana jest rama) na trzecie piętro, gdzie pracownicy stawiają silniki i mosty. Po zakończeniu cyklu na drugim piętrze nowe samochody wjeżdżają na ostatnią rampę obok biur na pierwszym piętrze. Produkcja gwałtownie rosła w każdym z trzech lat, z 19 000 w 1910 r. Do 34 000 w 1911 r., Osiągając imponujące 78 440 sztuk w 1912 r. A to dopiero początek, bo Ford już teraz grozi „zdemokratyzowaniem samochodu”.
Myśląc o tym, jak stworzyć wydajniejszą produkcję, przypadkowo trafia do rzeźni, gdzie obserwuje mobilną linię do krojenia wołowiny. Mięso tuszy rozwieszane jest na hakach poruszających się po szynach iw różnych miejscach rzeźni, rzeźnicy rozdzielają je, aż nic nie pozostaje.
Wtedy przyszedł mu do głowy pomysł i Ford postanowił odwrócić ten proces. Innymi słowy, oznacza to utworzenie głównej ruchomej linii produkcyjnej, która jest zasilana dodatkowymi liniami podłączonymi do niej na mocy umowy. Czas ma znaczenie - każde opóźnienie w którymkolwiek z elementów peryferyjnych spowoduje spowolnienie głównego.
7 października 1913 roku zespół Forda stworzył prostą linię montażową do montażu końcowego w dużej hali fabrycznej, w tym wyciągarkę i linę. Tego dnia 140 pracowników ustawiło się na około 50 metrach linii produkcyjnej, a maszyna była ciągnięta po podłodze za pomocą wyciągarki. Na każdym stanowisku dodawany jest do niego fragment konstrukcji w ściśle określonej kolejności. Nawet dzięki tej innowacji proces montażu końcowego zostaje skrócony z ponad 12 godzin do mniej niż trzech. Inżynierowie podejmują się zadania udoskonalenia zasady przenośnika. Eksperymentują z różnymi opcjami - z saniami, torami perkusyjnymi, przenośnikami taśmowymi, podwoziem holowniczym na linie i wdrażają setki innych pomysłów. W końcu, na początku stycznia 1914 r., Ford zbudował tak zwany przenośnik łańcuchowy bez końca, po którym podwozia ruszyły do robotników. Trzy miesiące później powstał system man high, w którym wszystkie części i taśma transportowa są umieszczone na wysokości pasa i zorganizowane w taki sposób, aby pracownicy mogli wykonywać swoją pracę bez poruszania nogami.
Wynik genialnego pomysłu
W rezultacie już w 1914 roku 13 260 pracowników Ford Motor Company zmontowało 720 samochodów w liczbach i słowach. Dla porównania, w pozostałej części przemysłu motoryzacyjnego 66 350 pracowników produkuje 286 770 samochodów. W 1912 roku Ford Motor Company wyprodukował 82 388 modeli T, po 600 egzemplarzy. W 1916 roku produkcja Modelu T wzrosła do 585 388, a cena spadła do 360 XNUMX USD.
Wielu zarzuca Fordowi zamianę ludzi w maszyny, ale dla przemysłowców obraz jest zupełnie inny. Niezwykle efektywne zarządzanie i rozwój pozwala tym, którzy potrafią uczestniczyć w organizacji procesu, a mniej wykształconym i niedoszkolonym pracownikom – sam proces. Aby zmniejszyć obroty, Ford podjął odważną decyzję iw 1914 roku podwyższył swoją pensję z 2,38 dolara dziennie do 1914 dolarów. W latach 1916-30, u szczytu I wojny światowej, zyski firmy podwoiły się z 60 do XNUMX milionów dolarów, związki zawodowe próbowały ingerować w sprawy Forda, a jej pracownicy stali się nabywcami ich produktów. Ich zakupy skutecznie zwracają część wynagrodzeń funduszu, a zwiększona produkcja utrzymuje niską wartość funduszu.
Nawet w 1921 roku Model T posiadał 60% rynku nowych samochodów. W tamtym czasie jedynym problemem Forda było wyprodukowanie większej liczby takich samochodów. Rozpoczyna się budowa ogromnego, zaawansowanego technologicznie zakładu, który wprowadzi jeszcze wydajniejszą metodę produkcji – proces just-in-time. Ale to już inna historia.
Tekst: Georgy Kolev
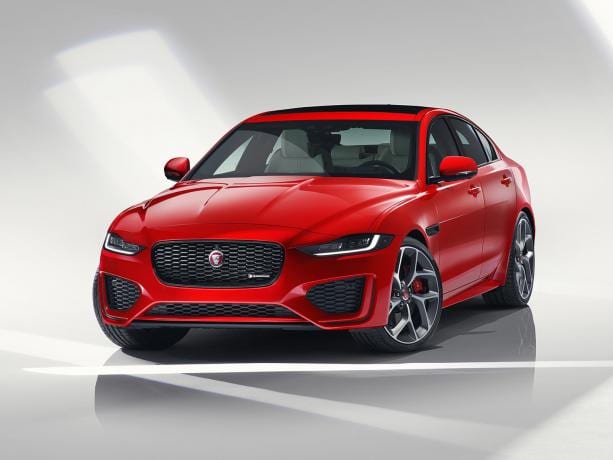
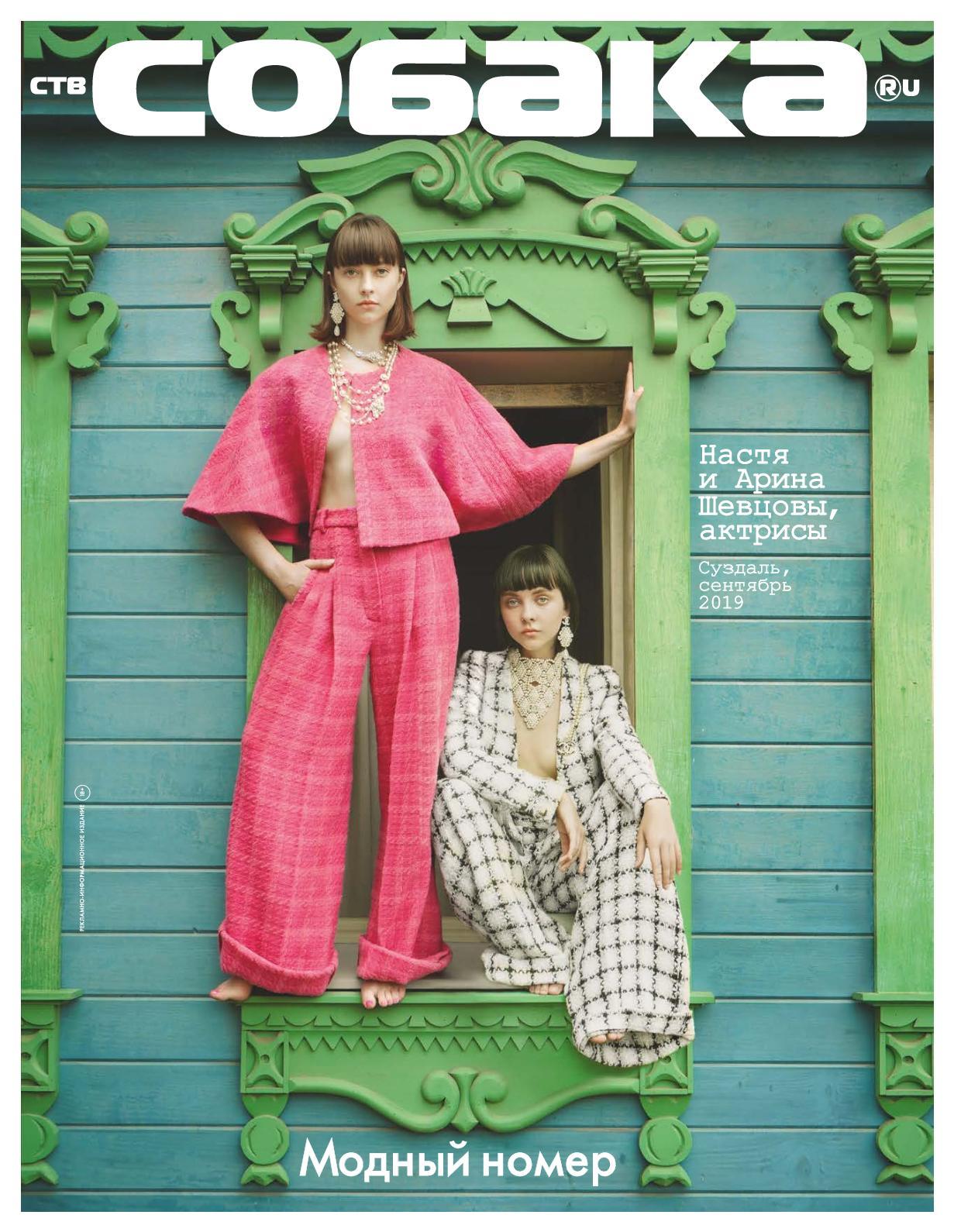