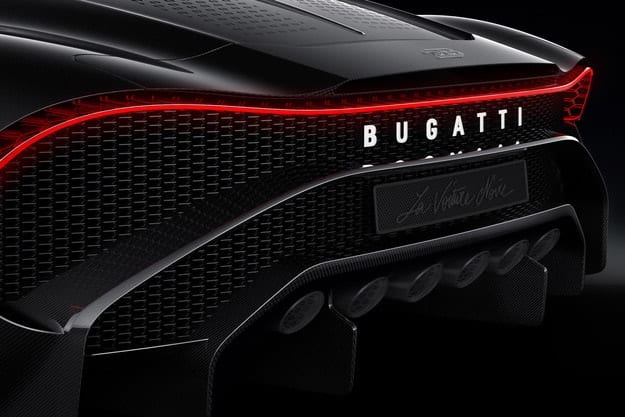
Bugatti: druk 3D w sercu Chiron
Francuski producent korzysta z tej technologii w 2018 roku w modelu Chiron Sport.
Od 2018 r. Producent z Molsheim stosuje technologię drukowania 3D do produkcji niektórych części hipersportowych Chiron, takich jak tytanowe końcówki wydechu Pur Sport i Super Sport 300+.
Podobnie jak Ettore Bugatti, założyciel marki tricolor, która regularnie demonstruje innowacje w projektowaniu swoich modeli (zawdzięczamy to głównie felgom aluminiowym i pustej przedniej osi), inżynierowie odpowiedzialni za rozwój nowych modeli Bugatti obejmują najnowsze innowacje. w budownictwie lub inżynierii w swoich dziełach. Jedną z nich jest technologia druku 3D, której zalety są już dobrze znane.
Bugatti zastosował tę technologię w 2018 roku w modelu Chiron Sport, który został następnie wyposażony w końcówki wydechowe z Inconel 718, twardego i lekkiego stopu niklowo-chromowego, szczególnie odpornego na ciepło (w tym przypadku stopu aluminium). Następujące modele marek (Divo, La Voiture Noire, Centodieci ...) również skorzystają z tego procesu produkcji w zakresie sprzedaży rur wydechowych.
Te elementy utworzone przy użyciu drukowania 3D mają kilka zalet. Z jednej strony są one bardziej odporne na ciepło i eliminują akumulację ciepła wytwarzaną przez 8,0-litrowy silnik W16 o mocy 1500 KM, a także są lżejsze niż dysze wykonane zwykłą metodą produkcji. (Chiron Sport waży tylko 2,2 kg, na przykład o 800 g mniej niż zwykła dysza).
W przypadku nowego Chiron Pur Sport Bugatti produkuje tytanowe dysze wylotowe z nadrukiem 3D, a producent wskazuje, że jest to „pierwsza widoczna metalowa część wydrukowana w 3D z homologacją do ruchu”. Ta dysza, o długości 22 cm i szerokości 48 cm, waży tylko 1,85 kg (łącznie z kratką i konserwacją), czyli około 1,2 kg mniej niż standardowy Chiron.
Specjalny system drukowania laserowego stosowany do drukowania 3D składa się z jednego lub więcej laserów, które z kolei topią warstwy pyłu o wielkości od 3 do 4 mikronów. 4200 warstw proszku metalowego układa się jeden na drugim i łączy ze sobą, tworząc dyszę wydechową Chiron Pur Sport, która wytrzyma temperatury powyżej 650 stopni Celsjusza, zapewniając podwójną izolację termiczną sąsiednich części.
Przed dokładną kontrolą i montażem w pojeździe elementy te zostaną w końcu specjalnie pokryte. Na przykład Chiron Sport jest szlifowany korundem i czarny lakierowany wysokotemperaturową farbą ceramiczną, natomiast Chiron Pur Sport i Super Sport 300+ są dostępne w szczotkowanym tytanie.
Gwarantując trwałość, ultralekkość i estetykę części, technologia druku 3D, nadal stosowana głównie w lotnictwie i kosmosie, wydaje się wreszcie znaleźć swoje miejsce wśród producentów samochodów, nawet najbardziej wymagających.
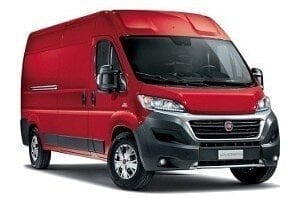
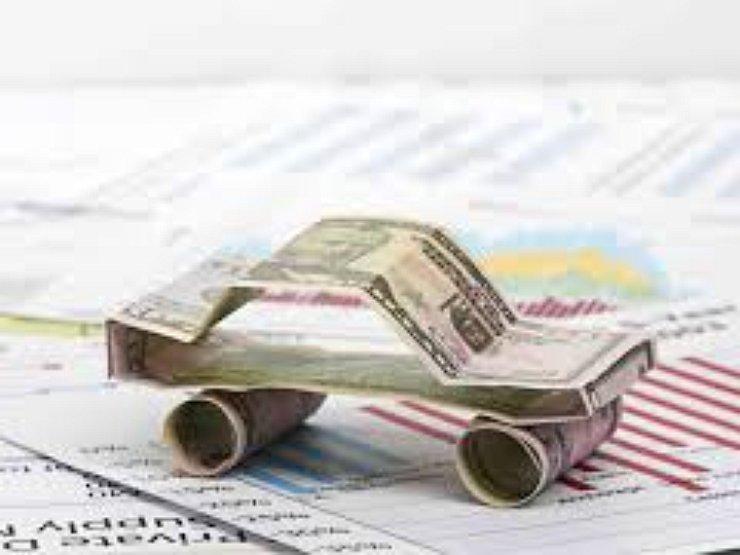